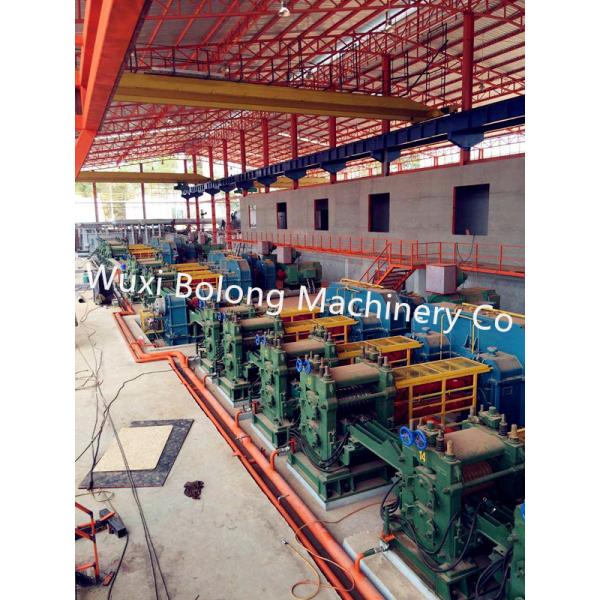
Cut To Length 12M Hot Rolling Machine With Hydraulic Billet Pusher Grouping
HOT ROLL MILL PROCESS EQUIPMENT
Design basis
1 Raw material spec: 100×100×2000mm
2 Final products spec: Φ10~Φ28mm hot-rolled deformed bar,
cut-to-length 12m
3 Hourly output: 10t/h
Rolling type and rolling mill configuration
1 Rolling mill layout type adopts semi-continuous.
2 To roll min. Section Φ10mm deformed bar based on 75×75mm
billets, rolling passes is of 15.
3 Adopt “one stand of service ” type to reduce rolling passes gradually.
4 There are total 11 stands of rolling mill in the whole production line,
including Φ400×1 rough rolling mill, Φ300×6 intermediate rolling mill
and Φ300×2×2 finishing rolling mill.
5 Rolling mill drive: Φ400×1 rough rolling mill is AC motor. Φ300×6
intermediate rolling mill is “one AC motor drives six”.
finishing rolling mill is “one DC drives two”
Φ300×2×2
6 The highest rolling speed of final products stands to roll Φ10mm
deformed bar is 8m/s.
Equipment characteristic
1. Rolling mill stand adopts pre-stressed type. This type is high
stiffness and easy to change roller.
2. The rolling mill’s driving applies reducer and the duplex adopt
two-grade reduction united gearbox. This type has following advantage:
low weight, small volume, economical space occupation, low cost and etc.
Gear-shaft material: 42CrMo forged, Wheel gear material ZG35CrMo,
the box is of structural parts.
3. Cooling bed entering adopts free of roller table pneumatic
entering type, which has the advantage of light equipment, simple, low
cost and easy maintenance compared with apron plate type entering
device.
4. End-cropping and multiple-length flying shear adopt
pneumatic clutch frequency controls speed, rotatory type. This type of
flying shear has the advantage of low motor power, simple electric
control and low investment compared with start-stop flying shear.
5. The bundling adopts mechanical pneumatic combined type
automatic machine, and the material for bundling is Φ6.5mm wire rod.
Process equipment list
No | Equipment name | Qty | Unit weight (t) | Total weight (t) | Main performance |
1 | Grouping bracket | 1 set | 5 | 5 | Type: hydraulic billet pusher grouping Bracket stored billet max. Qty: 40pcs Bracket stored billet max. Weight: 3.5t Billet pusher: Thrust: 25KN Pushing speed: forward 0.05m/s, backward 0.1m/s Stroke: 1350mm |
2 | Furnace charging roller table | 2 group s | 4.8 | 9.6 | Type: centralized driving, reversible Roller: φ240×650mm Roller spacing: 890mm Linear speed of roller surface:1m/s Driving motor: AC15KW |
3 | Billet pusher | 1 set | 3.5 | 3.5 | Type: hydraulic billet pusher Thrust: 100KN Stroke: 650mm Pushing speed: forward 0.05m/s, backward 0.1m/s Hydraulic cylinder: φ150/φ105mm System pressure: 10MPa Working oil pressure: 6.3MPa |
4 | Buffer | 1 set | 0.5 | 0.5 | Type: spring buffer |
5 | Feeding bracket | 1 set | 1 | 1 | Type: structural part |
6 | Billet out machine | 1 set | 5 | 5 | Type: car horizontal moving chain Thrust: 0.2KN Pushing speed: 0.875m/s Stroke: 4000mm Driving motor: AC7.5KW |
7 | Furnace out roller table | 2 group s | 4 | 8 | Type: centralized driving,reversible Roller: φ240×600mm Roller spacing: 1000mm Linear speed of roller surface:2m/s Driving motor: AC7.5KW |
8 | Working roller table before machine | 1 group | 8 | 8 | Type: centralized driving, reversible Roller: φ240×900mm Roller spacing: 1000mm Linear speed of roller surface:2.6m/s Driving motor: AC15KW |
9 | Φ400 rough rolling mill | 1 stand | 60 | 60 | Stand type: three-roll pre-stressed type Roller : φ400-φ350×800mm Roller max opening: 50mm Max. Rolling force: 1000KN Max. Rolling torque: 30×2KN.m Flywheel: φ1800mm Main motor: AC800Kw |
10 | Double-layer roller table | 1 set | 10 | 10 | |
11 | Intermediate roller table | 1 group | 5 | 5 | Type: centralized driving, reversible Roller: φ200×700mm Roller spacing: 1000mm Linear speed of roller surface:2.6m/s Driving motor: AC7.5KW |
12 | 1# end-cropping flying shear | 1 set | 8 | 8 | Type: pneumatic clutch, frequency controls speed, rotary type Cutting max. Section: 1500mm² Cutting temperature ≥850℃ Driving motor:YTSZ30KW |
13 | Φ300×6 intermediate continuous rolling mill group | 1 stand | 80 | 90 | Stand type: two-roll pre-stressed Roller: φ330-φ280×600mm Roller max. Opening: 30mm Max. Rolling force: 600KN Max. Rolling torque: 15×2KN.m Main motor: AC630Kw |
14 | Repeater | 4 sets | 1.5 | 6 | Type: structural part |
15 | Φ300×2 finishing continuous rolling mill | 2 group s | 20 | 40 | Stand type:pre-stressed type Roller: φ330-φ280×600mm Roller max. Opening:20mm Max. Rolling force: 250KN Max. Rolling torque: 4.5×2KN.m Main motor: DC450Kw |
16 | 2# end-cropping flying shear | 1 set | 8 | 8 | Type: pneumatic clutch, frequency controls speed, rotary type Cutting max. Section: 250mm² Cutting temperature ≥850℃ Driving motor:YTSZ30KW |
17 | Vertical loop | 1 set | Type: pneumatic loop up and down Loop-start height: 320mm | ||
18 | Remained heat treatment after rolling machine | 1 set | 2.5 | 2.5 | |
19 | Pinch roll | Type: pneumatic clamping,frequency controls speed Roller: φ240×60mm Linear speed of roller surface:4.5~9m/s | |||
20 | Multiple-length flying shear | 1 set | 8 | 8 | Type: pneumatic clutch, frequency controls speed , rotary type Cutting max. Section: 150mm Cutting temperature:≥600℃ Driving motor:YTSZ 37Kw |
21 | End-clamping roll | 2 sets | 2.5 | 5 | Type: pneumatic clamping, frequency controls speed Roller: φ240×60mm Linear speed of roller surface: 4.5~8m/s Driving motor:YTSZ11KW |
22 | Cooling bed entering device | 1 set | 35 | 35 | Type: non-roller table pneumatic entering Entering duration: 1.5s/time |
23 | Cooling bed | Type: step-by-step Effective area: 4.5×42m² Gear spacing: 90mm Fixed gear spacing: 500mm Movable gear spacing: 500mm Step duration: 2s/time Driving motor: AC55Kw | |||
24 | Alignment device | 1set | 3.5 | 3.5 | Type: chain single driving Roller: φ100×400mm Linear speed of roller surface:0.2m/s Driving motor: AC1.5KW |
25 | Cooling bed exit device | 1set | 30 | 30 | Type: hydraulic transverse support out type Rotary duration: 6s/time |
26 | Cooling bed run-out roller table | 5groups | 2 | 10 | Type: belt centralized driving Roller: φ200×700mm Roller spacing: 1000mm Linear speed of roller surface:2.5m/s Driving motor: AC7.5KW |
27 | Final product cutting machine | 1set | 10 | 10 | Type: upper cutting type hydraulic shear Final product Cutting force: 1600KN Blade width: 800mm Blade opening: 160mm Cutting times: 6times/min |
28 | Roller table after cutting | 1group | 5 | 5 | Type: belt centralized driving Roller: φ200×700mm Roller spacing: 1000mm Linear speed of roller surface:2.5m/s Driving motor: AC7.5KW |
29 | Cut-to-length baffle | 1set | 0.2 | 0.2 | Type: pneumatic lifting Baffle opening: 150mm |
30 | Bar transfer machine run-in roller table | 1group | 6 | 6 | Type: belt centralized driving Roller: φ200×700mm Roller spacing: 1000mm Linear speed of roller surface:2.5m/s Driving motor: AC7.5KW |
31 | Bar transfer machine | 1set | 5 | 5 | Type: pneumatic lifting, chain-type transfer bar Chain pitch: 38.1mm Chain spacing: 1600mm Transfer speed: 0.6m/s Driving motor: AC11Kw |
32 | Collection alignment device | 1set | 0.275 | 0.275 | Type: pneumatic pushing plate type |
33 | Collection device | 1set | 2.5 | 2.5 | Type: double channel rotary type Collection weight: 3500kg Channel changing rotary duration: 6.8s Driving motor: AC7.5KW |
34 | Collection run-out roller table | 1group | 4.5 | 4.5 | Type: chain centralized driving Roller: φ200×400mm Roller spacing: 800mm Linear speed of roller surface:0.52m/s Driving motor: AC7.5KW |
35 | Bundling machine | 1group | 4 | 4 | Type: pneumatic elevating and falling, mechanical rotation united type Bundling max. Outer diameter:350mm Bundling one bunch time: 8s Driving motor: AC1.5KW |
36 | Bundling machine run-out roller table | 1set | 3 | 3 | Type: chain centralized driving Roller: φ200×400mm Roller spacing: 1000mm Linear speed of roller surface:0.52m/s Driving motor: AC7.5KW |
This is our customer's plan, we will according your specific requirements to design and manufacture the hot rolling mill.
Wuxi Huadong Industrial Electrical Furnace Co.,Ltd.
Our company is located at the northeast of Wuxi, Jiangsu Province, with only 2.5 hours of driving distance to Shanghai Pudong International Airport, and the traffic is very convenient.
Wuxi Huadong Industrial Furnace Co., Ltd is a comprehensive enterprise integrating scientific research & development, engineering designing, system integration, equipment installation and sales & services. Our company is dedicated to professional manufacture the production lines for casting of various non-ferrous metals and heat treatment since 1989.
The production lines for casting non-ferrous metals supplied by our company is complete in categories, specifications and types, mainly capable of casting metals including copper and copper alloys, also related to non-ferrous metals such as magnesium, aluminum and zinc etc. The casting modes include horizontal continuous casting, vertical casting and upward casting; By using our production lines, customers can get billet products with sections of near-the-net-shape dimensions and shapes, including 8 major categories i.e. plates, strips, rods, foils, tubes, bars and shapes. Heat treatment equipments include multiple types of electric resistance furnaces or combination, such as well type, box type, bogie-hearth type, bell type, protective-atmosphere type, vacuum bright type, strong-convection circulation type etc. For casting production lines and heat-treatment equipments, our company can also provide various types of spare parts (furnace shells, melting grooves, water jackets, iron cores, crystallizers, special refractory, temperature measurement devices, transformers, reactors, electric resistance heating elements, and mechanical parts etc.); Our company can also provide cold-processing equipments such as drawing mills and cold-rolling mills for tubes, rods and shapes, as well as scrap metal balers etc.
Our company can develop, design, and manufacture equipments for specific production lines according to customers' requirements, provide complete services of solutions; Committed to quality, quality priority covers the whole process of designing, purchasing ,manufacturing, production, installation and after-sales services etc. We are doing our best to realized most advanced in technology, most reasonable in configuration, most superior in quality, and most inexpensive in cost. We strictly follow the requirements of ISO9000 quality system, achieving first-class product quality.
Choosing Wuxi Huadong Electric Industrial Furnace Co. ,Ltd as the
partner means choosing trust and guarantee, and the correction
choice is the safeguard for the smooth operation of your
undertakings and reliable return of your investment.
Wuxi East China Furnace Co. ,Ltd would like to
cordially welcome friends from home and abroad for visiting and
guidance.